What post-processing is required for glass bottles after molding?
Jul 22,2025
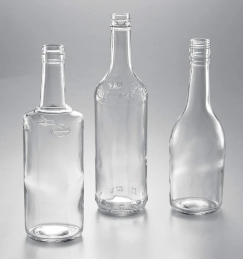
After glass bottles are formed and annealed, they undergo a series of post-processing steps to ensure quality, functionality, and suitability for various applications. These processes mainly include: Fine processing, quality inspection, surface decoration, and cleaning and packaging These steps are detailed below:
I. Fine Processing: Optimizing the Neck and Structure
The neck is the critical interface between the bottle and the outside world, directly affecting sealing and ease of use, requiring special attention:
-
Neck Finishing
- Cutting/Polishing: The formed neck may have burrs or unevenness and needs to be cut with a special tool or ground with a grinding wheel to create a smooth edge (e.g., the neck of a beverage bottle must perfectly match the cap to prevent leakage).
- Thread Processing: For bottles requiring screw caps (e.g., mineral water bottles, condiment bottles), standard threads are processed on the outer side of the neck by rolling or molding to ensure smooth cap tightening.
- Sealing Surface Treatment: Some glass bottles (e.g., infusion bottles, reagent bottles) require a flat sealing surface on the inner side of the neck to achieve sterile sealing with a rubber stopper or aluminum cap.
-
Special Structure Processing
- For graduated glass bottles (e.g., reagent bottles, measuring cups), graduation lines need to be marked via laser engraving or screen printing to ensure accuracy (error usually ≤1%).
- Some oddly shaped bottles (e.g., bottles with handles) require welding or one-piece molding of the handle; the welded area needs to be annealed again to eliminate stress and prevent breakage.
II. Quality Inspection: Screening Qualified Products
Multi-dimensional inspection is used to eliminate substandard products, ensuring safety. This includes:
-
Appearance Defect Inspection
- Manual or machine vision inspection: Identifying defects such as bubbles, cracks, stones (unmelted raw material particles), spots, and deformation (e.g., cracks in food-grade glass bottles may lead to contamination).
- Light Transmittance Inspection: Using strong light to check for impurities or cloudy streaks affecting transparency (commonly used for high-end cosmetic bottles and pharmaceutical glass bottles).
-
Size and Performance Inspection
- Dimensional Accuracy: Using calipers, gauges, etc., to measure parameters such as neck diameter, bottle height, and wall thickness to ensure compliance with design tolerances (e.g., the diameter error of threaded necks needs to be controlled within ±0.1mm, otherwise, it may not match the cap).
- Sealability Test: Using negative pressure or positive pressure methods—after sealing the bottle, creating a vacuum (or pressurization) to observe for leaks (e.g., carbonated beverage bottles need to withstand a certain internal pressure; failure to meet sealing requirements will lead to leakage and bulging).
- Physical Properties: Impact resistance tests (drop tests), temperature resistance tests (sudden cooling and heating to check for breakage), etc., are performed on glass bottles for critical applications (e.g., beer bottles, infusion bottles).
III. Surface Decoration: Enhancing Functionality and Aesthetics
Based on the application (e.g., packaging, decoration), surface treatment is applied to glass bottles. Common methods include:
-
Printing and Labeling
- Screen Printing: Printing trademarks, ingredient descriptions, patterns, etc., on the bottle body (suitable for large areas or simple patterns).
- Heat Transfer/Water Transfer: Transferring complex patterns to the bottle body, suitable for curved or oddly shaped bottles (e.g., perfume bottles, gift bottles).
- Laser Engraving: Engraving permanent text or patterns on the surface (no ink, suitable for food and pharmaceutical bottles).
-
Coating and Film Deposition
- Wear-Resistant Coating: Spraying a transparent resin coating to enhance the scratch resistance of the glass surface (e.g., repeatedly used beverage bottles).
- Functional Film Deposition: Metal film deposition (e.g., aluminum film) to enhance light shielding (used for pharmaceutical bottles requiring UV protection); hydrophobic film deposition for easy cleaning (e.g., oil-stained bottles).
-
Sandblasting and Etching
- Mechanical Sandblasting: Using a grinding wheel or sandblasting to create a matte texture, enhancing slip resistance and aesthetics (e.g., wide-mouth cosmetic bottles).
- Chemical Etching: Using hydrofluoric acid or other solutions to corrode the surface, creating three-dimensional patterns or translucent effects (often used for high-end craft bottles).
IV. Cleaning and Packaging: Ensuring Cleanliness and Transportation Safety
-
Cleaning and Disinfection
- Glass bottles containing food or pharmaceuticals need to undergo water washing (removing surface dust), ultrasonic cleaning (removing impurities from crevices), and high-temperature sterilization (e.g., 121℃ steam sterilization) to ensure sterility and no residue.
- Ordinary packaging bottles need to be dried to prevent mold growth during storage.
-
Packaging and Shipping
- Grouped by specifications, separated and packaged with cardboard, foam, or plastic dividers to prevent damage during transportation.
- Some high-end products use custom gift boxes to enhance product value.
Summary
Post-processing is a crucial step in transforming glass bottles from "prototypes" to "finished products." It ensures safety and functionality (e.g., sealing, strength) and enhances market competitiveness through decoration. Different types of glass bottles (e.g., food bottles, medicine bottles, craft bottles) have different post-processing priorities—for example, medicine bottles emphasize sterility and chemical stability, while gift bottles emphasize the sophistication of appearance decoration.
PREVIOUS:
Contact Us
E-mail :
TomasYan@wzglass.com
Phone/WhatsApp:
+86-0775-6658866
Address:
Min'an Town Daily Ceramic Industrial Park, Beiliu City, Guangxi Province, China

Get in touch
Are you interested in our products or services? Contact us immediately, our experts will provide you with professional services!
*Please leave your specific personal information, and we will have a product consultant contact you later
Address
Min'an Town Daily Ceramic Industrial Park, Beiliu City, Guangxi Province, China