Glass bottle specification standardization
Mar 28,2025
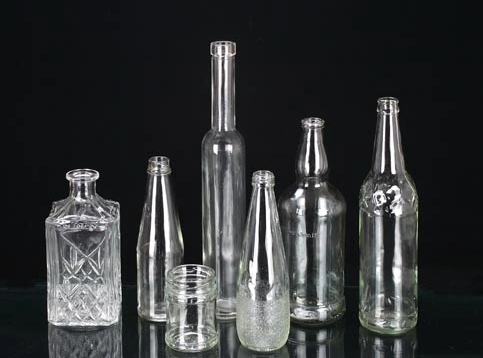
Foshan Nanhai Jianhua Glass Co., Ltd. achieves standardization of glass bottle specifications primarily through the following key steps:
- Raw Material Selection and InspectionStrictly select main raw materials such as quartz sand, soda ash, and limestone, ensuring their purity and particle size meet requirements. For example, the suitable particle size of quartz sand is 0.25-0.5mm, and the iron content must be low to ensure the glass is pure, uniform, and free of defects such as sand, streaks, and bubbles. Each batch of raw materials undergoes rigorous inspection; only qualified materials are used in production, guaranteeing product consistency and stability from the source.
- Batching PreparationAccurately weigh various raw materials and mix them according to precise formulas, ensuring the batch is uniformly mixed and chemically stable. This helps to make the glass melt uniform in the melting process, thus ensuring that the glass bottle's performance and quality meet standards.
- Mold Design and ManufacturingDesign glass bottle molds of various specifications and shapes according to market demand and customer requirements. The mold's size accuracy and manufacturing quality directly affect the quality of the glass bottle's formation; therefore, the company uses advanced processing equipment and technology to ensure that the mold's size tolerance is kept to a minimum, guaranteeing that the produced glass bottles have uniform specifications and shapes.
- Melting Process ControlThe batch is placed in a tank furnace or pool furnace for high-temperature heating, typically at 1550-1600℃, to form a uniform, bubble-free liquid glass that meets forming requirements. During the melting process, parameters such as temperature, time, and furnace atmosphere are strictly controlled to ensure the stability of the glass melt quality.
- Molding Process SpecificationsMainly uses the molding method, applying the blow-blow method to form small-mouth bottles and the press-blow method to form wide-mouth bottles. When using automatic bottle-making machines for high-speed molding, there are strict requirements for the weight, shape, and uniformity of the gob. By precisely controlling parameters such as the temperature in the feeder, the gob meets the molding requirements, ensuring that the produced glass bottles have stable volume, weight, and shape, with uniform wall thickness.
- Annealing TreatmentAnnealing glass bottles and jars reduces residual stress to an allowable value, usually in a continuous annealing furnace with a mesh belt. The annealing temperature can reach 550-600℃. By using forced airflow circulation heating, a uniform temperature distribution is created in the cross-section of the furnace, forming an air curtain that limits longitudinal airflow movement and ensures uniform and stable temperature in each zone of the furnace. This ensures that the internal stress of the glass bottle meets the standard, improving its mechanical strength and stability.
- Surface TreatmentGenerally, surface treatment of glass bottles and jars is done by coating at the hot and cold ends of the annealing furnace. Hot-end coating involves placing the hot (500-600℃) formed bottles in an environment of vaporized tin tetrachloride, titanium tetrachloride, or tin butyl tetroxide, allowing the metal compound to decompose and oxidize into an oxide film on the hot bottle surface. This fills in micro-cracks on the glass surface and prevents the formation of micro-cracks, improving the mechanical strength of the glass bottles and jars. Cold-end coating uses monostearate, oleic acid, polyethylene emulsion, silicone, or silane to spray a lubricating film on the surface of the bottles and jars at the annealing furnace outlet (approximately 100-150℃), improving the surface's abrasion resistance, lubricity, and impact strength.
- Quality InspectionComprehensive quality inspection of glass bottles is performed using various testing methods, including checking the weight, capacity, size tolerances of the bottle mouth and body, internal stress resistance, thermal shock resistance, and stress relief. For high-speed, high-volume products such as beer bottles and beverage bottles, automatic inspection equipment such as pre-selectors, bottle mouth inspectors, crack detectors, and wall thickness measuring devices are also used to promptly identify and remove defective products, ensuring that product quality meets standards.
- Packaging StandardizationGlass bottles are packaged using standardized packaging materials and methods, such as corrugated cardboard boxes, plastic boxes, and pallet-based packaging. This facilitates transportation and storage, protects glass bottles from damage during transportation, and improves loading, unloading, and handling efficiency.
In addition, Foshan Nanhai Jianhua Glass Co., Ltd. actively participates in the formulation and revision of industry and national standards, paying attention to the latest technologies and standards in the domestic and international glass bottle industry. The company continuously improves and refines its production processes and quality control systems to ensure that its glass bottle products consistently meet standardized requirements in terms of specifications and quality, maintaining its competitiveness in the industry.
Contact Us
E-mail :
TomasYan@wzglass.com
Phone/WhatsApp:
+86-0775-6658866
Address:
Min'an Town Daily Ceramic Industrial Park, Beiliu City, Guangxi Province, China

Get in touch
Are you interested in our products or services? Contact us immediately, our experts will provide you with professional services!
*Please leave your specific personal information, and we will have a product consultant contact you later
Address
Min'an Town Daily Ceramic Industrial Park, Beiliu City, Guangxi Province, China