How to ensure the quality and safety of glass bottles for alcoholic beverages?
Feb 11,2025
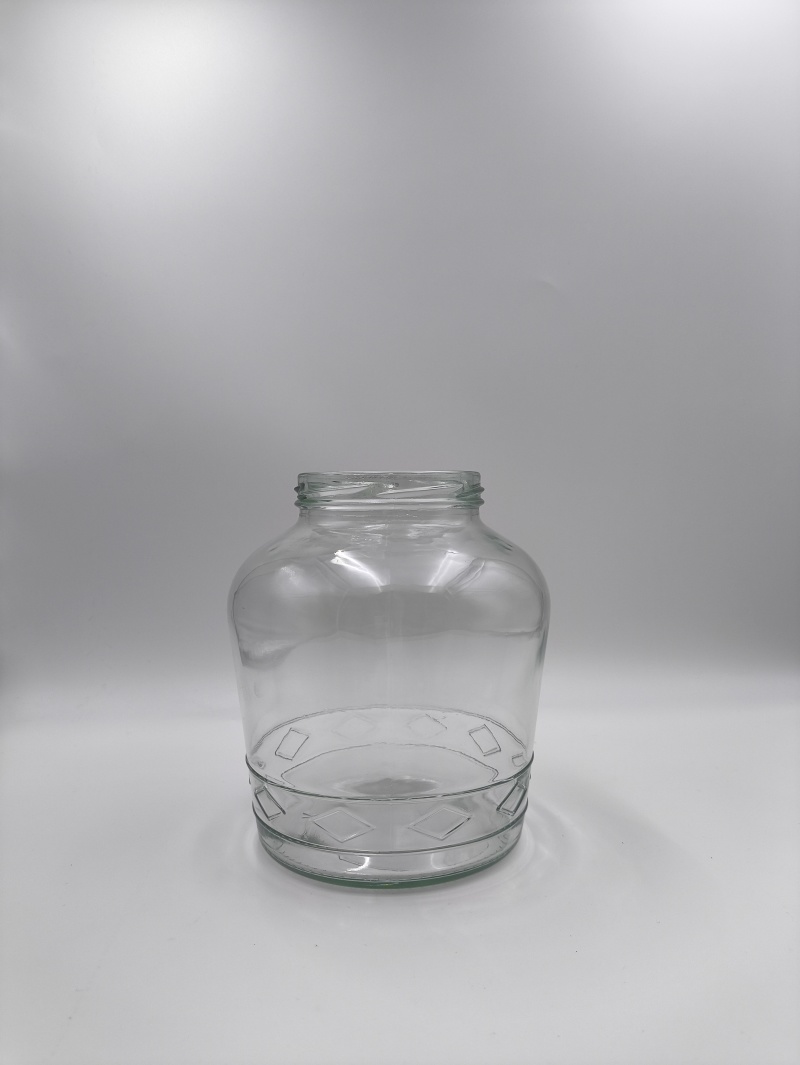
Ensuring the quality and safety of glass bottles for alcoholic beverages involves multiple aspects such as raw material selection, production process control, and quality inspection, as detailed below:
Raw Material Selection
- Strictly select basic raw materials: Use high-purity quartz sand, soda ash, limestone, and other basic raw materials to ensure that their impurity content is extremely low. For example, the silicon dioxide content in quartz sand should be above 99% to ensure the transparency and stability of the glass, reducing defects such as bubbles and cracks caused by impurities.
- Focus on the quality of auxiliary materials: For auxiliary materials such as clarifiers and colorants, strict quality control is required. For instance, the purity and performance of the clarifier directly affect the bubble removal effect in the molten glass; high-quality clarifiers can effectively improve the purity of the glass.
Production Process Control
- Accurately control furnace temperature: The furnace temperature must be stabilized between 1500℃-1600℃; temperatures that are too high or too low will affect the uniformity and fluidity of the molten glass, leading to issues such as uneven thickness and uneven surfaces of the glass bottles.
- Optimize forming process parameters: Adjust the pressure, time, and other parameters of blowing or pressing accurately according to different bottle shapes and specifications. For example, when blowing wine bottles, precise control of the blowing pressure and time can ensure the roundness of the bottle body and uniform wall thickness.
- Ensure proper annealing process: During the annealing process, the temperature curve must be strictly followed for heating and cooling, with a general cooling rate controlled at 5℃-10℃/minute to eliminate internal stress in the glass and prevent the bottles from breaking during subsequent use.
Quality Inspection
- Appearance Inspection: A combination of manual visual inspection and machine vision inspection is used to conduct a comprehensive check of the bottle's appearance. Inspection items include whether the bottle body has bubbles, scratches, cracks, or missing corners, whether the bottle mouth is flat and smooth, and whether the bottle surface has stains or impurities.
- Dimensional Accuracy Inspection: Use calipers, micrometers, and other measuring tools to measure key dimensions such as the height, diameter, and wall thickness of the bottles, ensuring that the dimensional deviation is within the specified range. For example, the height tolerance of beer bottles is generally controlled within ±2mm, and the wall thickness tolerance is within ±0.5mm.
- Physical Performance Testing
- Compressive Strength Testing: Apply pressure to the bottles using a compressive testing machine to detect the maximum pressure they can withstand. Generally, the compressive strength of liquor bottles should not be less than 1.2MPa to ensure they can withstand certain pressure during transportation and storage.
- Impact Resistance Testing: Use drop ball impact testing machines and other equipment to simulate the impacts that bottles may encounter during actual use, testing their impact resistance. Qualified glass bottles for alcoholic beverages should be able to withstand impacts from steel balls of certain heights and weights without breaking.
- Internal Stress Testing: Use a polarizing stress meter to detect the internal stress distribution of the bottles, ensuring that the internal stress meets standard requirements to avoid self-explosion due to excessive internal stress.
Packaging and Transportation
- Choose appropriate packaging materials: Use cushioning materials such as foam and plastic film for individual packaging of bottles, then place the bottles in sturdy cartons or plastic turnover boxes, filling the boxes with foam boards, molded pulp, and other cushioning materials to prevent the bottles from colliding with each other during transportation.
- Standardize transportation loading and unloading operations: During transportation, choose appropriate transportation tools and routes to avoid severe vibrations, collisions, and high temperatures that could adversely affect the bottles. During loading and unloading, use professional equipment such as forklifts and cranes, handling gently and prohibiting rough handling.
Warehouse Management
- Control the storage environment: The warehouse should be kept dry and ventilated, with the temperature controlled between 15℃-25℃ and relative humidity between 40%-60%, to avoid quality degradation of the bottles due to moisture and temperature changes.
- Reasonable stacking and piling: Bottles should be categorized and stacked according to specifications and batches, with a moderate stacking height, generally not exceeding 5 layers, to prevent the bottom bottles from breaking due to excessive pressure. Additionally, regular inspections and inventory checks of the stock bottles should be conducted to promptly identify and address any quality issues.
Contact Us
E-mail :
TomasYan@wzglass.com
Phone/WhatsApp:
+86-0775-6658866
Address:
Min'an Town Daily Ceramic Industrial Park, Beiliu City, Guangxi Province, China

Get in touch
Are you interested in our products or services? Contact us immediately, our experts will provide you with professional services!
*Please leave your specific personal information, and we will have a product consultant contact you later
Address
Min'an Town Daily Ceramic Industrial Park, Beiliu City, Guangxi Province, China