Different glass bottle forming methods each have their own advantages and disadvantages.
Feb 19,2025
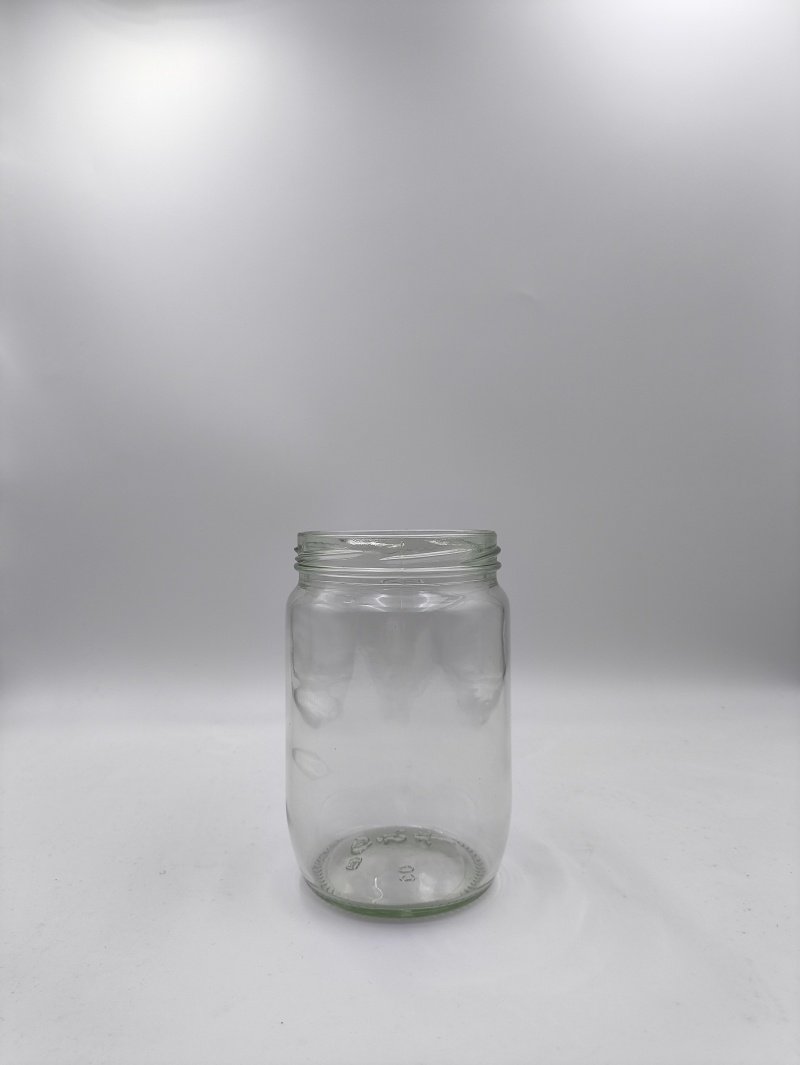
The following are the advantages and disadvantages of different forming methods for glass bottles:
Pressing method
- Advantages
- Precise shapeAble to produce glass bottles with accurate shapes. For bottles with patterns, designs, or specific shape requirements, the pressing method can effectively meet design requirements.
- Simple processThe operation is relatively simple, requiring no complex equipment and technology. The production process is easy to control, with high production efficiency, suitable for mass production.
- Disadvantages5
- Shape limitationsThe internal cavity shape of the product has certain limitations and cannot be expanded downwards; otherwise, the punch cannot be removed. The inner cavity sidewalls cannot have protrusions or recesses, making it impossible to produce some special-shaped bottles.
- Difficult to produce thin wallsIt is difficult to produce products with thin walls and long internal cavities in the vertical direction. For some bottles that require thin wall designs, the pressing method may not meet the requirements.
- Surface defectsThe surface of the product is not smooth enough, often having spots and mold seams, requiring subsequent processing to improve surface quality.
Blow molding method
- Advantages
- Uniform bottle bodyThe bottle body is relatively uniform, and wrinkles and other phenomena are not easily produced. Compared to the blowing method, it can achieve better wall thickness uniformity.
- Lighter weightBlown bottles are lighter, 20%-50% lighter than bottles made by the blowing method with the same strength.
- High production efficiencyThe forming speed is fast, production efficiency is high, product quality is good, and it is suitable for mass production.
- Disadvantages
- Uneven thicknessThe entire forming process is divided into two steps. During the processing, the temperature of the material will decrease, making it easy to produce uneven thickness in the bottle body.
- Difficult to control dimensional accuracyThere are high requirements for the weight error of the glass material drops. If the weight exceeds or is below the standard value, defects such as burrs at the mouth or insufficient mouth may occur.
Centrifugal casting method
- Advantages
- Suitable for large componentsIt can manufacture large glass bottles with thin and thick walls, which is difficult for other forming methods, meeting the needs of some special fields for large glass containers.
- Low internal stressUnder the action of centrifugal force, no shrinkage holes or scars are produced inside the casting, resulting in very low or almost no internal stress, with high surface finish and good product quality.
- Small machining allowanceCompared to stationary molds, the machining allowance of the produced blank can be significantly reduced. When precision requirements are not high, it can produce parts that do not require machining, saving raw materials and processing steps.
- Disadvantages
- Complex equipmentThe required equipment is relatively complex, with high investment costs and longer production cycles, leading to higher component costs.
- Shape limitationsIt is difficult to produce cast plastic parts with complex shapes, which imposes certain limitations on the shape design of bottles.
Drawing method
- Advantages
- Uniform wall thicknessIt can produce glass tubes with uniform wall thickness, ensuring the uniformity of the wall thickness when further processed into bottles, with high mechanical strength.
- Suitable for specific productsIt is suitable for producing glass bottles that require high uniformity of wall thickness and need slender shapes, such as tubular glass injection vials.
- Low risk of particle contaminationDuring the production process, the risk of particle contamination is low, which is a significant advantage for containing substances sensitive to particle contamination, such as pharmaceuticals.
- Disadvantages
- Single shapeUsually, it can only produce relatively simple-shaped glass bottles, making it difficult to create bottles with complex shapes and structures.
- Relatively low production efficiencyCompared to pressing and blow molding methods, the drawing method has a slower production speed and relatively low production efficiency, making it unsuitable for large-scale, high-efficiency production needs.
Contact Us
E-mail :
TomasYan@wzglass.com
Phone/WhatsApp:
+86-0775-6658866
Address:
Min'an Town Daily Ceramic Industrial Park, Beiliu City, Guangxi Province, China

Get in touch
Are you interested in our products or services? Contact us immediately, our experts will provide you with professional services!
*Please leave your specific personal information, and we will have a product consultant contact you later
Address
Min'an Town Daily Ceramic Industrial Park, Beiliu City, Guangxi Province, China